The result is over the years the cowl vent opening gets rusted bad. Here you can see what it looked like when I started poking at it.
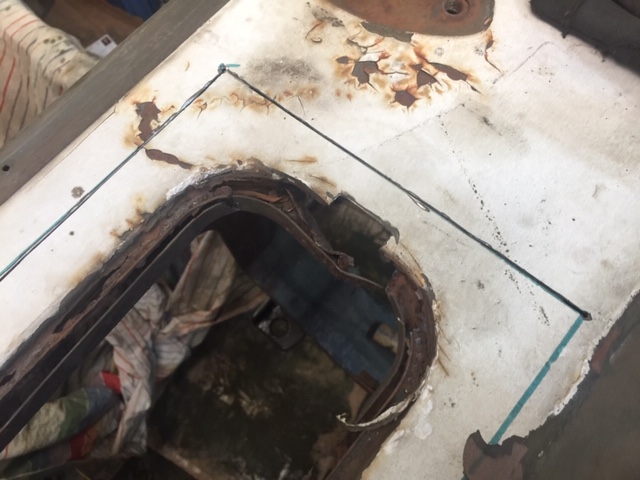
It’s not possible that I can see to work with the rusted vent opening. So, my solution is to cut it out. Then I will create a new opening in a sheet of metal on the workbench and add a lip to the opening that the vent can settle over. I plan on doing something like F18hornetm did in his 1953 M37 post. This link page 6 - http://www.g741.org/PHPBB/viewtopic.php ... ent+repair
Here is the whole area marked out and ready to cut out:
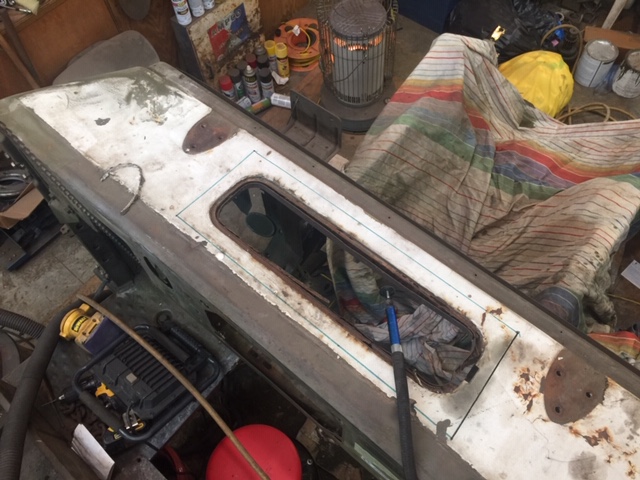
After going to it with the air cut off tool you can see the removed cowl.
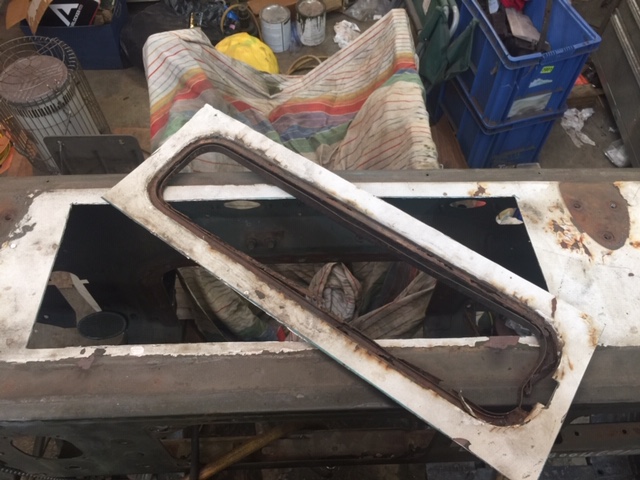
The old vent that was with the truck was also rusted a good bit. It might could have been worked over and used, but some years back I had purchased an NOS vent to use. I cut off all the sides of the old vent only leaving the top cover. I have this flexible moldable plastic tape that I used to bend in the curve of the inside of the vent top. I took this flexible tape to the point of my anvil and marked that spot with blue tape the place on the nose of the anvil that matches the curve of the vent top.
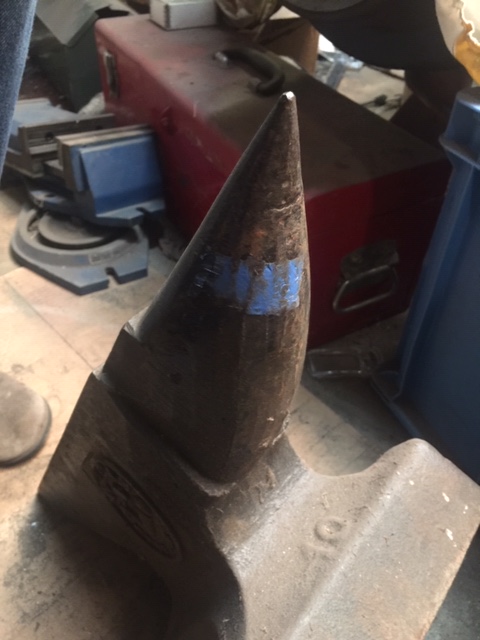
Curve Tool is the blue piece laying in the old vent lid. The NOS vent is to the left. The pieces of metal I heated and bent and will use to make a lip are on the right.
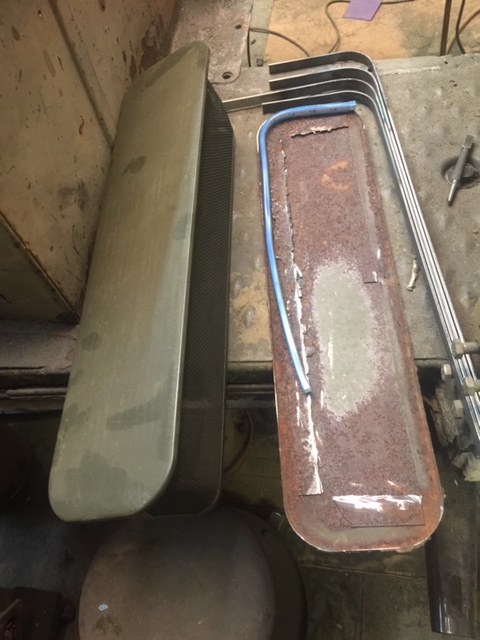
Here is a closeup of the curves I created. The bottom one was the first one I bent and played with it too much and might have to make another one. The next step is to cut the metal pieces up, jig them together and weld them.
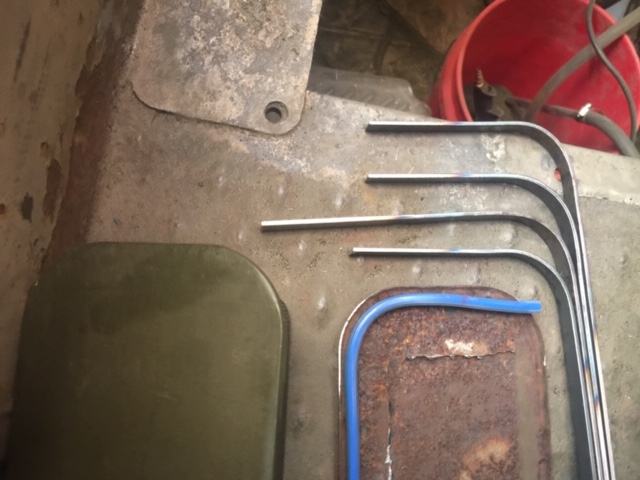
More updates as I make progress.